前言
通过前面的推文介绍,咱们已经知道了制备好的透射样品是必须能够对电子束透明,即电子束能够穿透样品的,要有能够供透射电镜表征的“薄区”,且一般薄区要求厚度在100nm以下。
怎样将样品制备成厚度100nm以下呢?
需要经过哪些步骤?
本期小编将带大家了解一下哦!
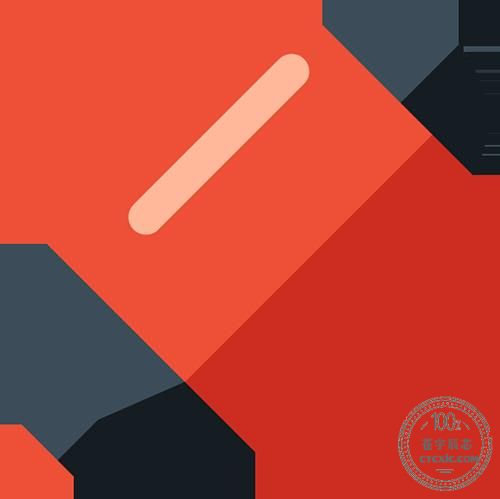
切割取样
I
机械磨抛1
I
切圆片
I
机械磨抛2
I
预减薄
I
最终减薄
I
薄区检查
1
切割取样
(样品厚度:1mm左右)
根据样品取样要求,将大块的样品切割成厚度1mm左右的小尺寸块体,一般常采用的工具为线切割、低速锯等。
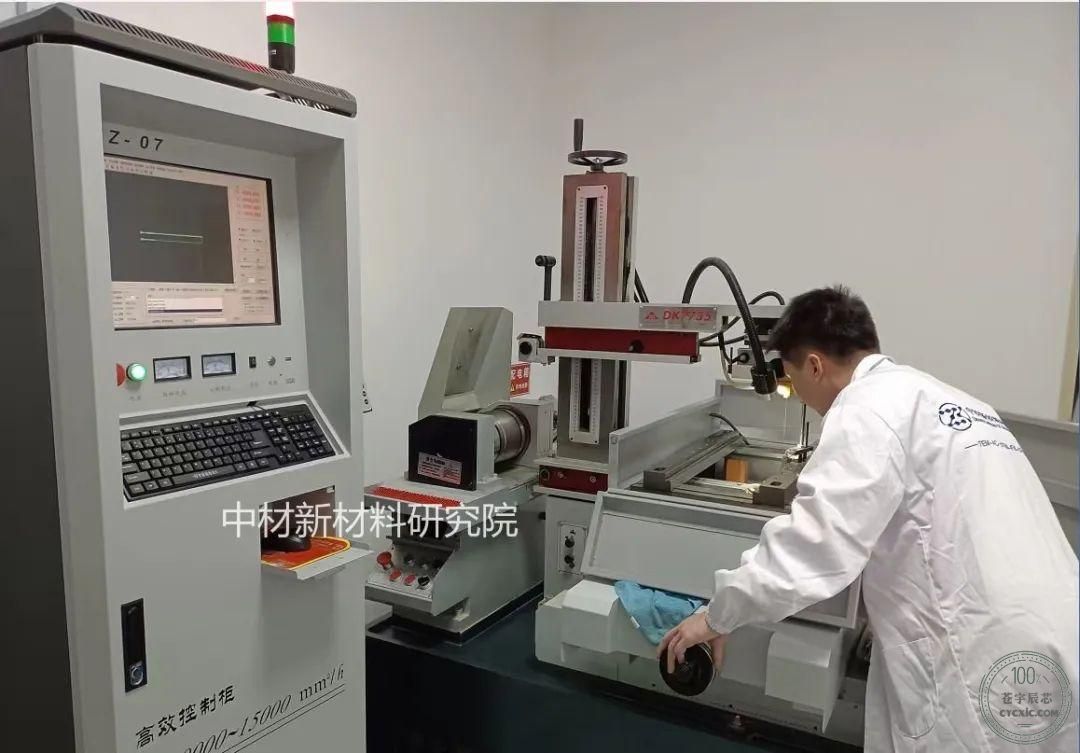
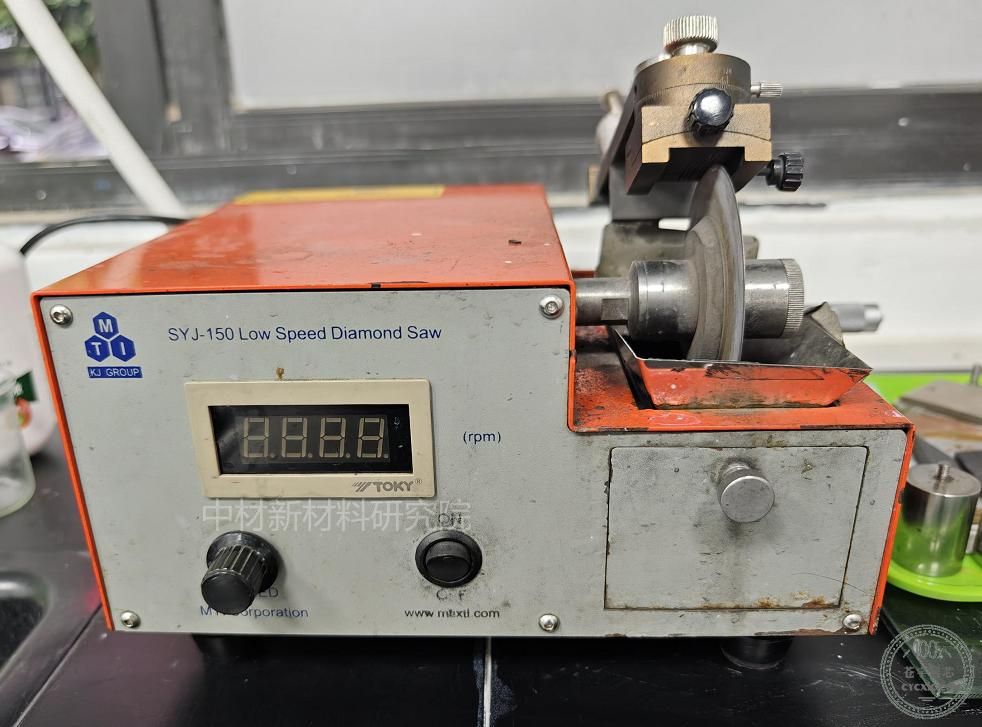
线切割 低速锯
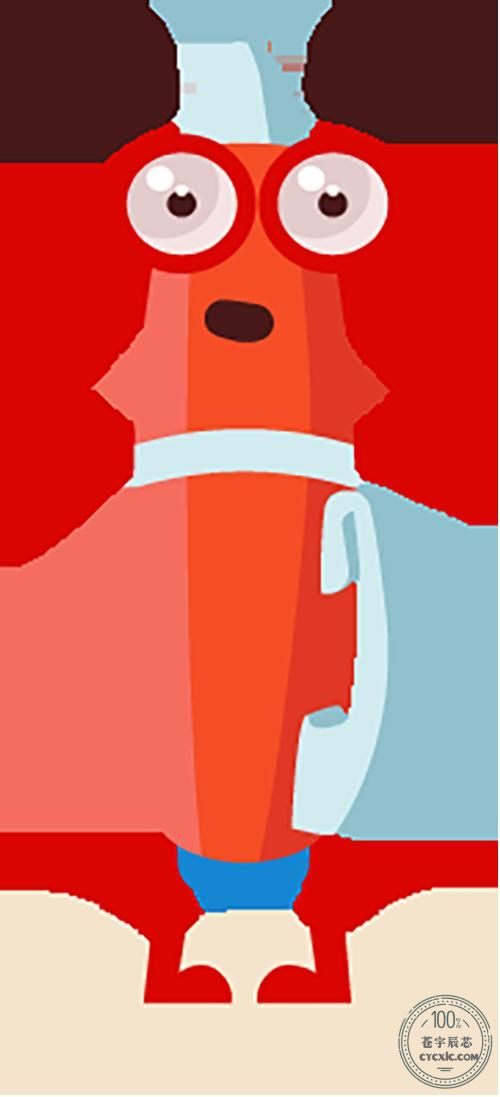
2
机械磨抛1
(样品厚度:100μm左右)
通过磨抛机或者手动磨抛的方式,将样品磨至厚度100微米左右的薄片,磨抛过程控制好样品的平整度。
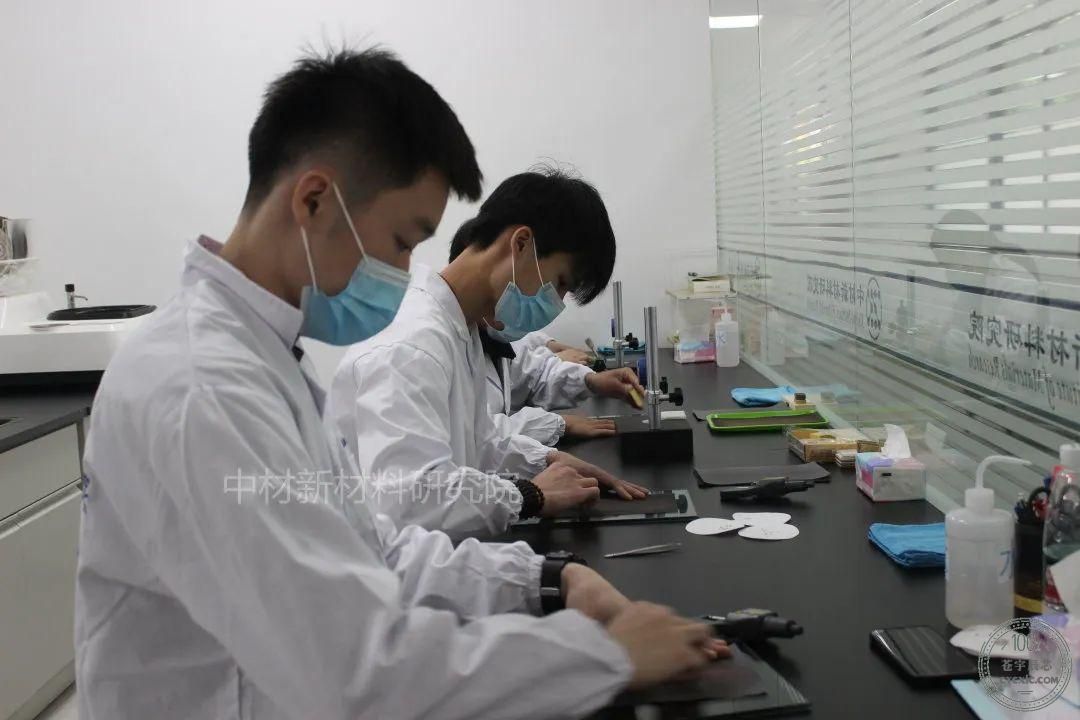
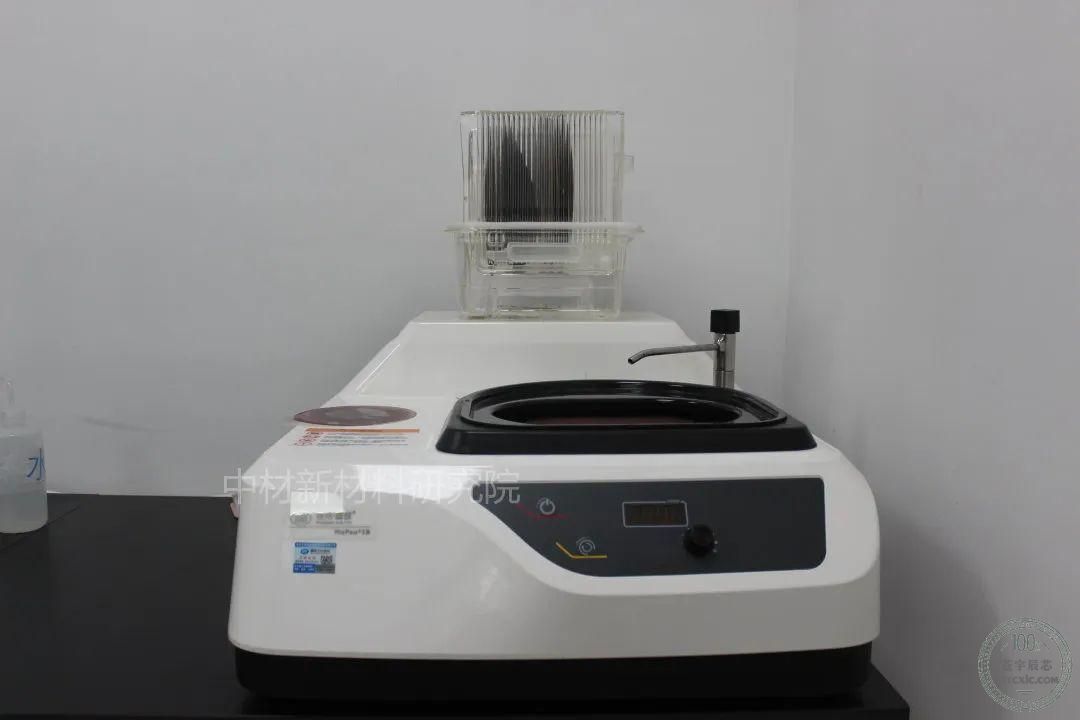
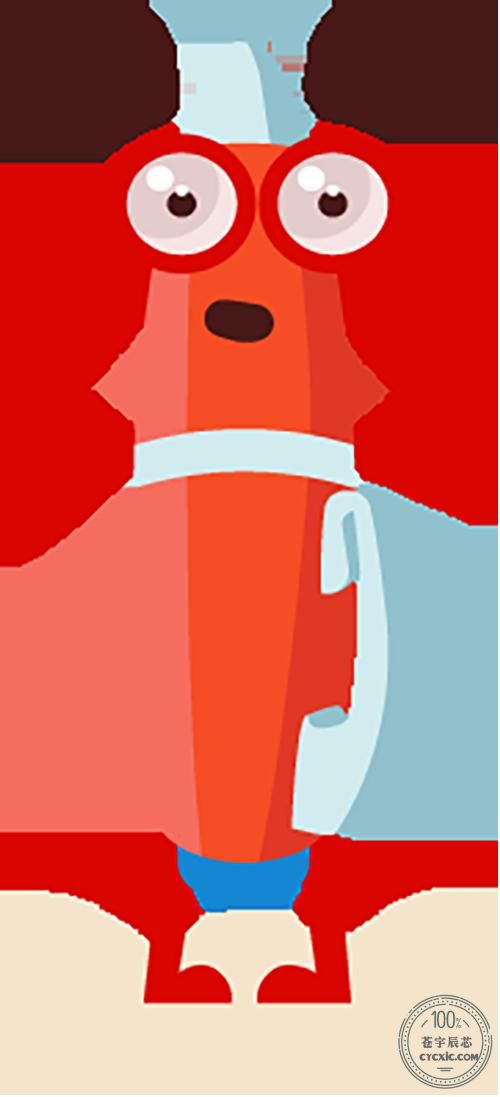
3
切圆片
(样品厚度:保持前一步100μm左右)
使用冲孔仪将前一步磨抛好的100μm厚的样品,机械冲出一个φ3mm的圆片,一般延展性比较好的样品会采用此方式;
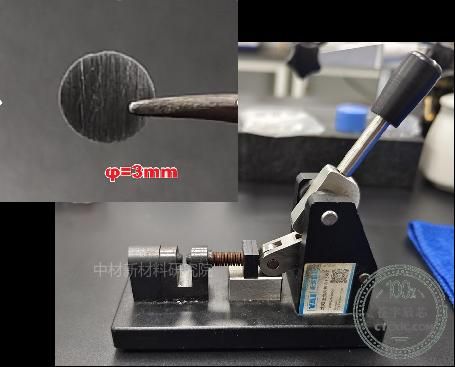
冲孔仪直接冲出φ3mm圆片
但对于比较脆或容易碎的样品,比如陶瓷、非晶条带等,采用直接冲孔的方式极易破坏样品;针对这类样品可以先采用粘环的方式,然后使用专业刀具手工切圆片,将边缘多余处和毛刺切除掉。
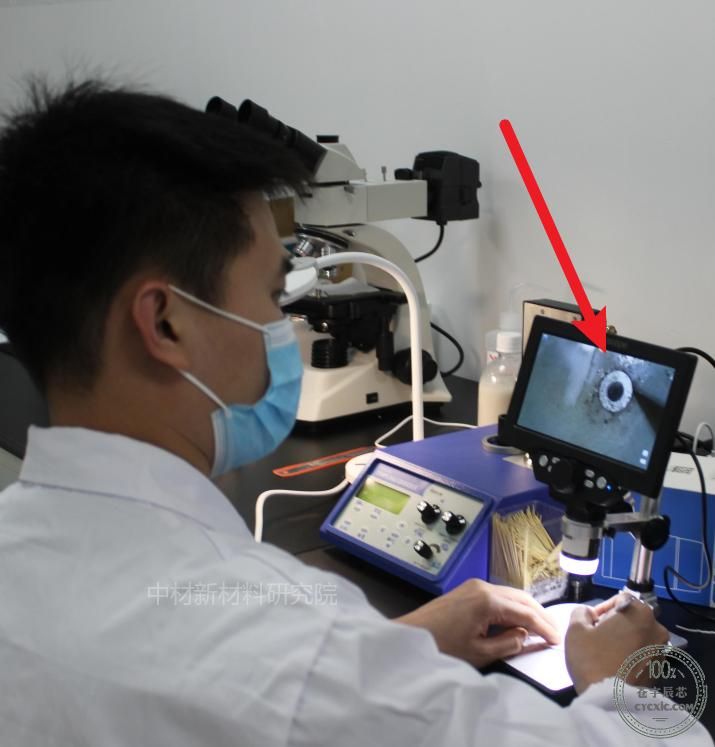
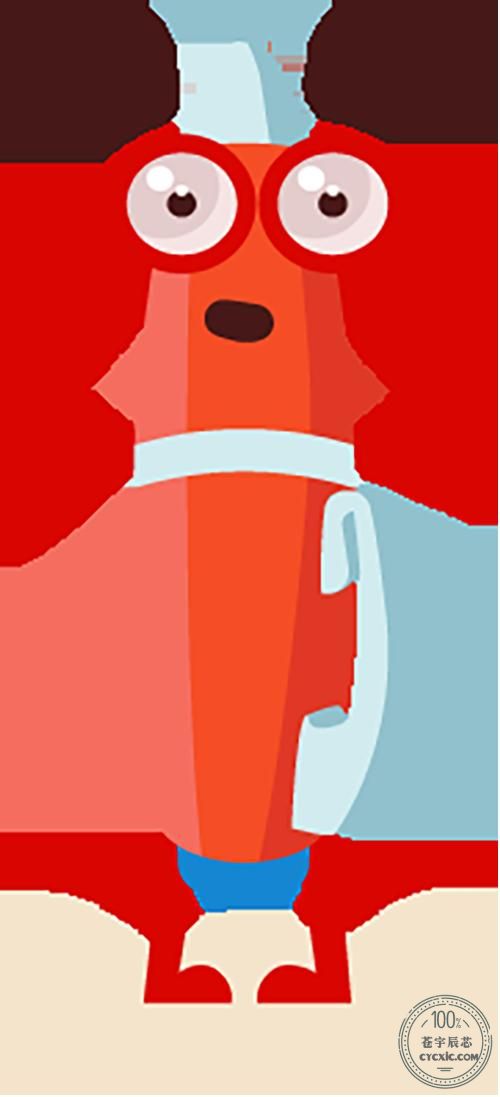
4
机械磨抛2
(样品厚度:30-40μm左右)
通常,所有的机械抛光顺序都相同,总是逐级降低“磨粒”尺寸,最后再用最小尺寸的研磨剂,确保最终厚度大于最小尺寸磨粒引起的损伤层深度的2倍。
该步骤将使用不同目数的砂纸,从粗到细,继续对样品进行磨抛,根据样品性质不同,将样品磨至30-40微米左右。一般最后一道常使用2000目砂纸。
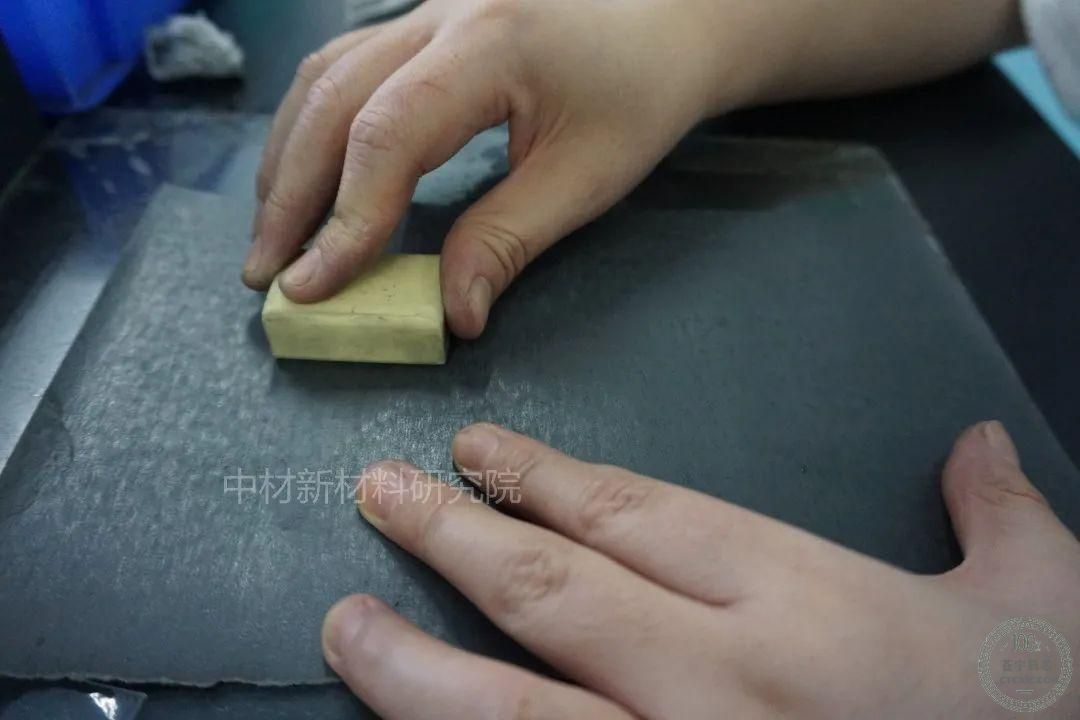
手工磨样
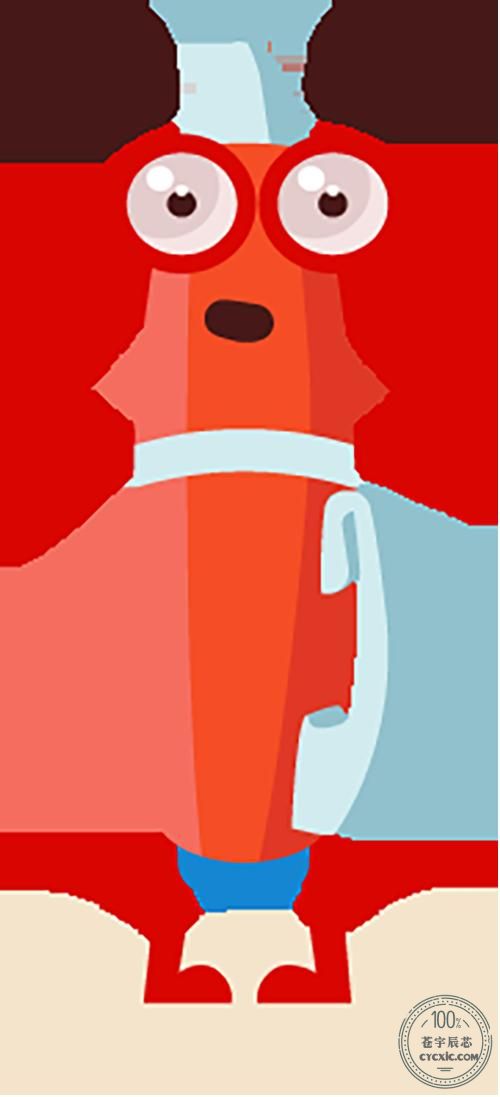
5
预减薄
(样品厚度:中心薄,整体厚度不变)
这个过程目的是使圆片中心变薄,同时要使样品表面的损伤最小。
这个过程产生的任何损伤都必须在最终减薄过程中去掉(除非你对缺陷感兴趣),常用一种叫凹坑仪的设备进行预减薄。
当然,这个步骤并不是必须的。
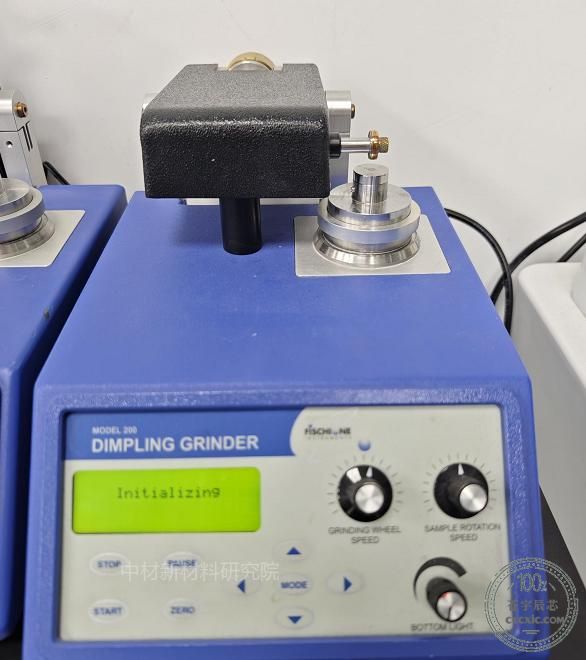
凹坑仪
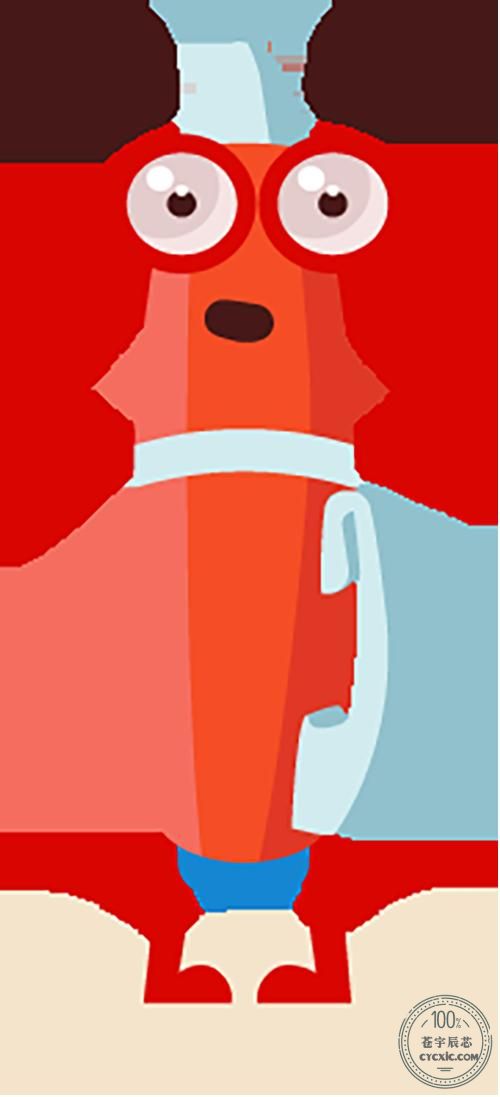
6
最终减薄
(样品厚度:中间穿孔、边缘厚)
最终减薄是要做出可以供透射电镜检测的薄区,通常需要制造出孔洞,薄区出现在孔洞边缘。
方式常用的一般有2种:离子减薄和电解双喷。
其中,电解双喷只能用于导电样品,例如金属和合金;这个方式相对比较快(快则几分钟即可)。
毫无疑问,多练习才能做好电解双喷,但是要重复温度、电解液的化学性质、外加电压、抛光液流速等正确的条件,只能通过反复试验来实现。所以,对于一个样品而言,双喷可没有想象中的那么简单哦。
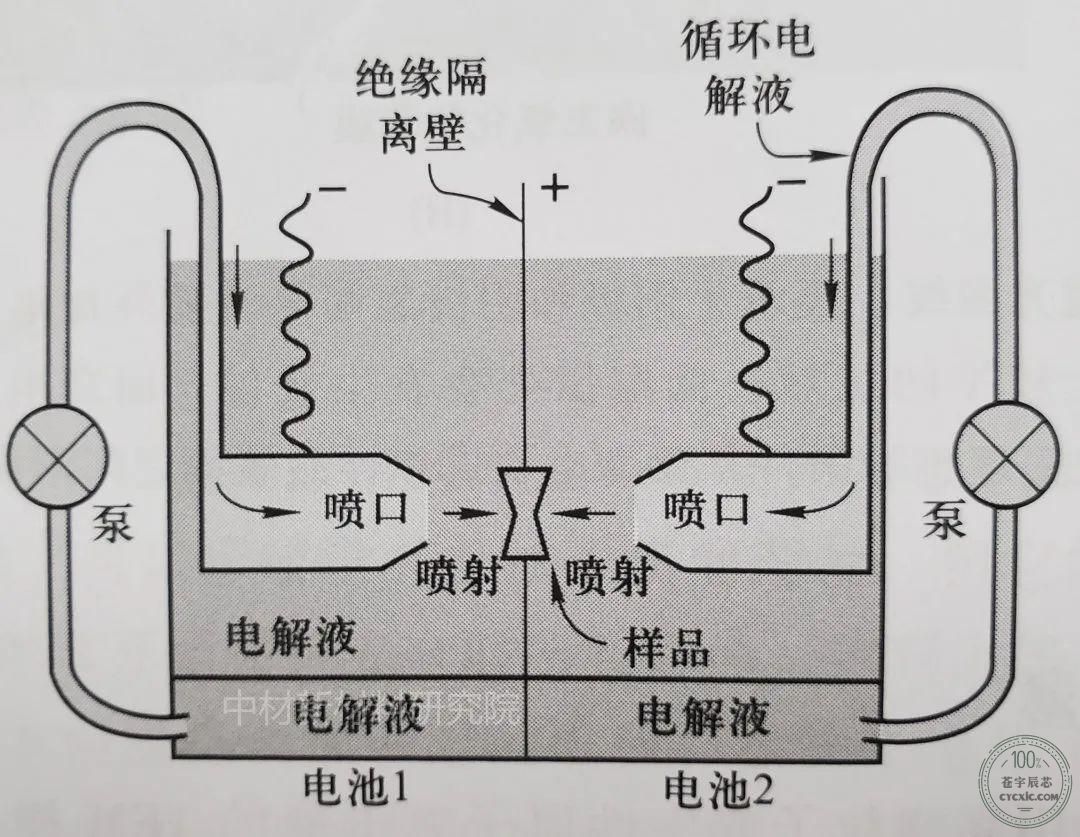
双面喷射式的电解抛光示意图
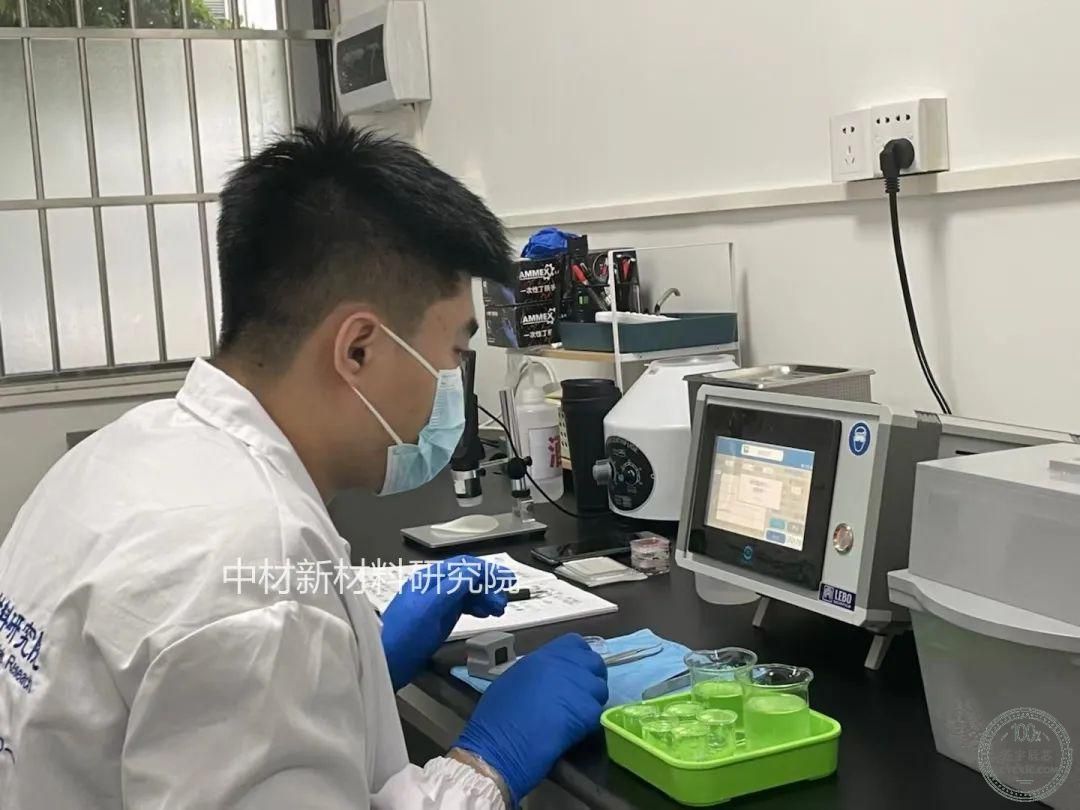
电解双喷操作中
离子减薄是使用在高能离子或中性原子轰击薄的TEM样品(常用的是氩离子),并使材料溅射下来直至薄到能在TEM中进行观察;
离子减薄是使用比较广泛的一种最终减薄方式,可用于陶瓷、复合材料、多相半导体和合金以及许多截面样品。
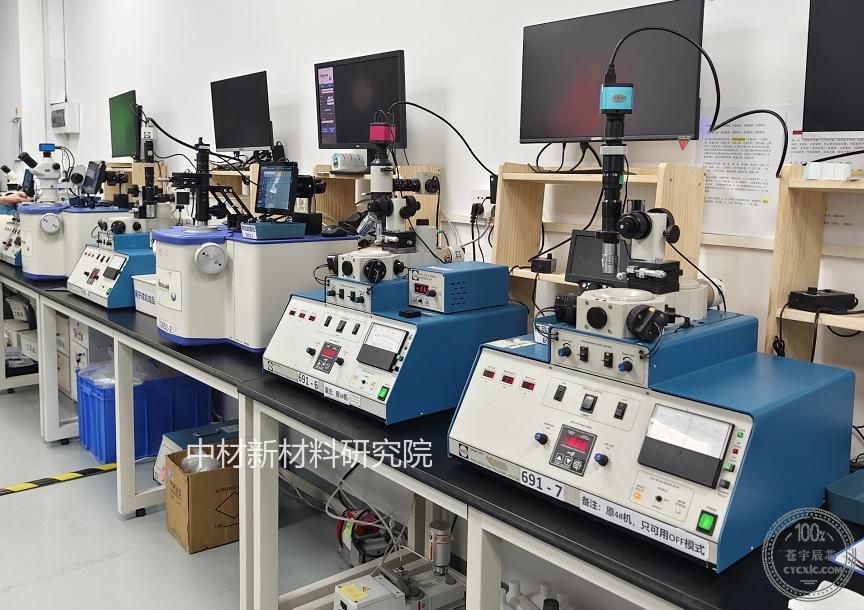
离子减薄仪
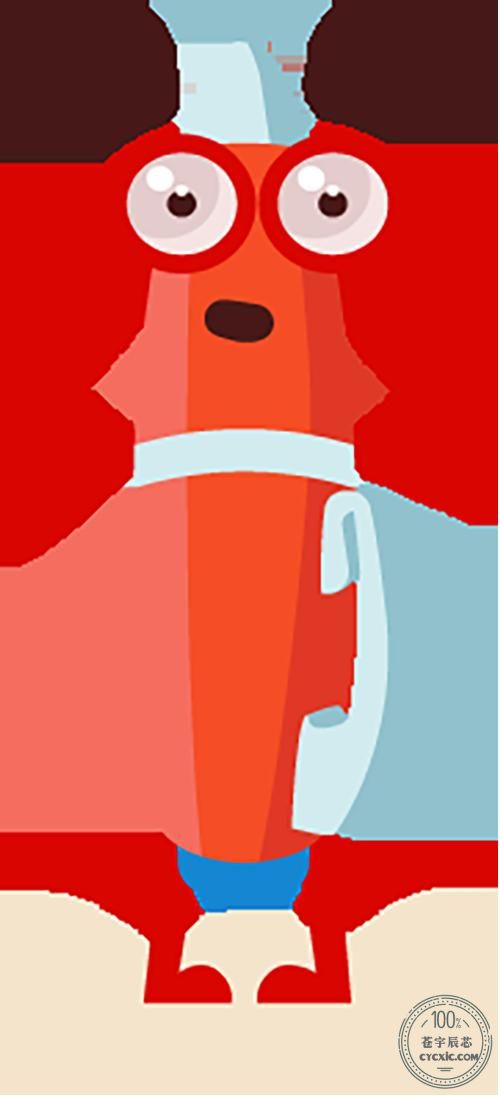
7
薄区检查
(样品厚度:中间穿孔、边缘厚)
样品制备好后,可利用肉眼、光学显微镜、扫描电子显微镜、透射电子显微镜等进行薄区质量检查,筛选出质量较好的样品用于后续的透射检测。
当然,这一步也不是必需的。
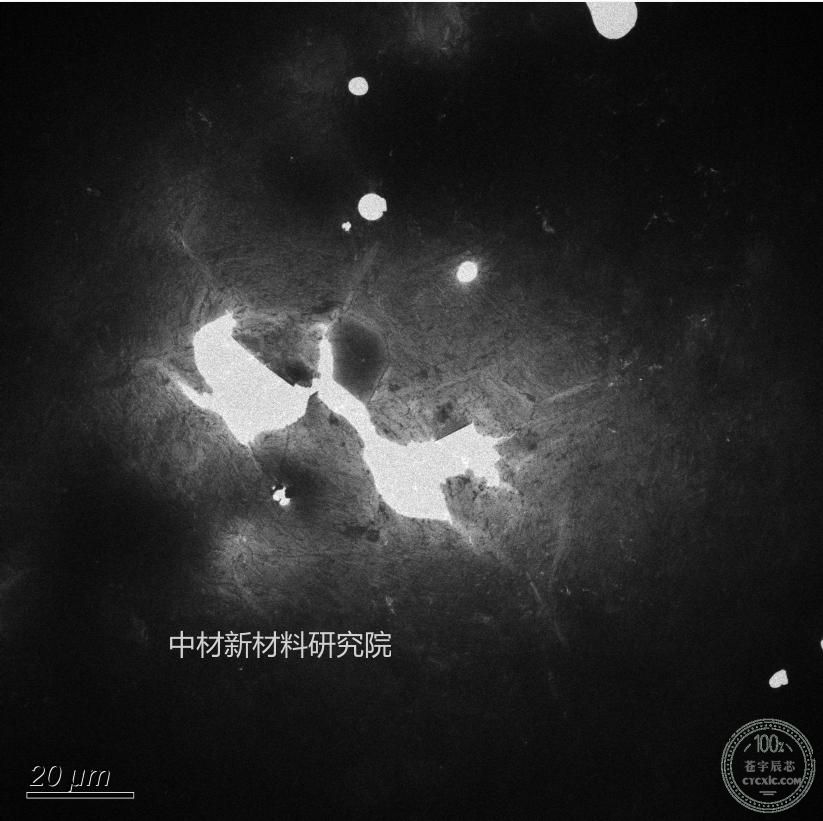
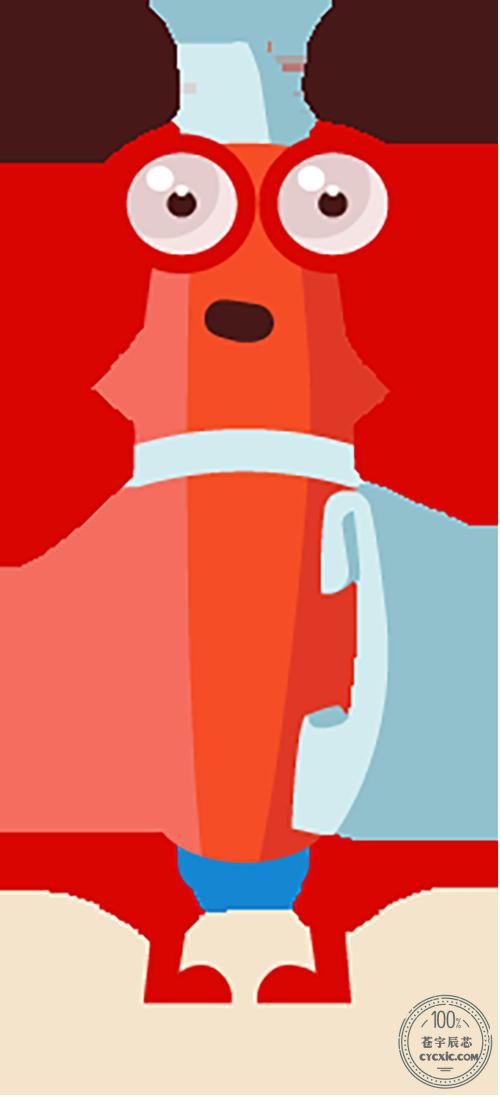